Brief Introduction to DH Quick-Heavy-Cold-Pipe-Bend Technology Lee Shengnan / Deputy General Manager of Dehan Intellectual Technology Co., Ltd. date: 2017-07-01
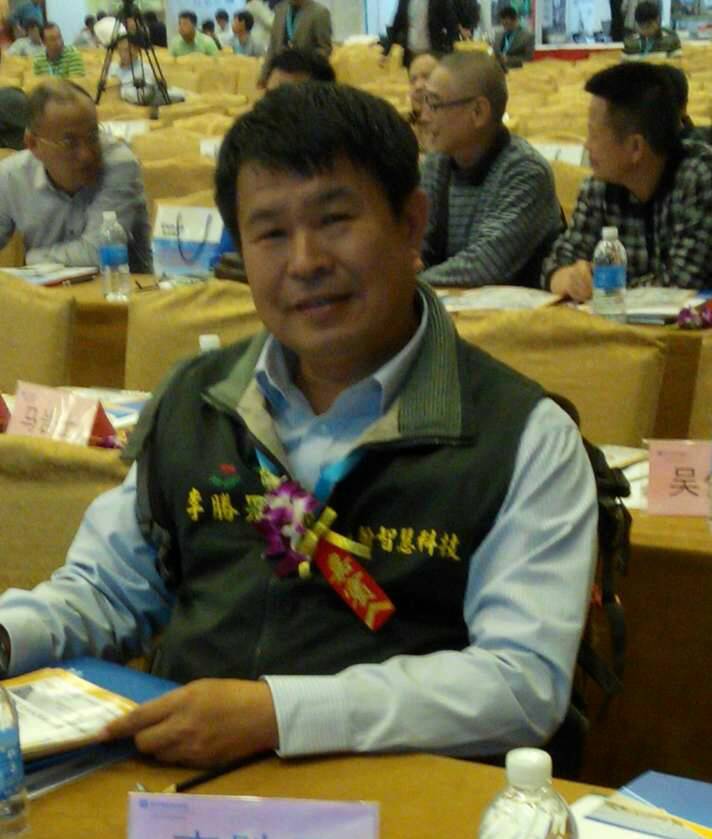
Note: The readers shall know that traditional version is original, most content of this paper was translated from it by software. Forword Metal piping is widely used in various industrial constructions, such as petrochemical industry, steel industry, electronics industry, shipbuilding and so on. The piping of steel pipelines is the most common, and the main components are divided into straight pipes, elbows, and valves ,etc. Straight pipes and elbows are made of steel pipes of specifications (outer diameter, pipe thickness, etc.), occupying the vast majority of piping work. The straight pipe and the elbow must be welded together to ensure the joint quality. The overall cost of the piping, in addition to the cost of the pipe, also includes welding manpower/machine tools/materials/inspection, etc. The process is complex, and the relative cost is high and the construction is slow. How to reduce the cost of piping, and effectively improve the quality of finished piping, shorten the installation speed of pipelines, and meet the requirements of rapid construction, that is, the main improvement goal of the next generation of piping construction/engineering. The scope of this paper is mainly based on petrochemical plant pipelines, and other industrial pipelines. Keywords: quick-heavy-cold-bending, quick bending, dehan, elbow, pipe bending 1. The traditional piping construction methods - advantages & disadvantages
The main features of heavy-duty pipelines in petrochemical plants are high internal pressure, high wall thickness, high material strength, and high danger of the contents of the pipeline. Therefore, it is impossible to take joints with the thread and must be welded. In this paper, the general discussion is mainly based on petrochemical plant pipelines. Other industrial pipelines are of course applicable, even the small pressure inside the pipeline. The piping is generally classified as an installation work at the construction site. In addition to valves, flanges and supports, the materials are mainly two types of pipes and elbows. Of course, insulation and instrumentation are not included here. As the length of the pipe is longer or the elbows is more, the consumption of the straight pipe and the elbow is more, the more the welding, the longer the time required, and the more the number of inspections. 1.1 Main items of piping work
In the work of piping, the main work items are three sub-items of material procurement, pipeline prefabrication (in prefabrication plant or contractor’s shop), site installation. Material procurement => Pipeline prefabrication => Site Installation These three major items should take a lot of time and cost. In this paper, we will discuss the pipelines that can be purchased from the engineering market are generally used ,and exclude the special material/diameter pipelines. In the site installation, the expected ratio of pipeline prefabrication to on-site installation is about 6:4 to 7:3, depending on the circumstances of the case, it may be lower. The higher the proportion of pipeline prefabrication work, the lower the workload on the site, and usually means that the work will be faster and smoother. The pipeline prefabrication work is carried out in the contractor's shop/factory. The working environment in the factory is relatively stable, and it is less subject to weather disturbance. The operating tools are more complete (such as cranes, stackers, welders, wheel cutters, straighteners, etc.). The labor utilization rate and production efficiency are also high, and it is easy to command. Generally, the quality of pipeline prefabrication is higher than the quality of on-site installation, and it is easy to inspect and overhaul. Owners and supervisors also prefer pipeline prefabrication. If the amount of pipeline prefabrication can be increased, and the quality of the prefabricated product is improved, and the cost is lowerized, the piping construction will undergo major changes. (1) Material procurement: It is divided into two major categories: straight pipe and elbow. Straight pipe is easier in stacking and less likely to be damaged. When the elbow material is delivered, it has already been processed (such as bending diameter, angle, including wall chamfer/grinding, etc.). It is generally not recommended to stack it to avoid damage, so it usually requires a relatively large space to stack and storage. When large project is implemented, elbows are usually stacked everywhere in shop . If the elbow delivery sequence is not properly arranged, it will also delay the follow-up work (prefabrication or on-site work). (See Fig. 1-1) (2) Pipeline prefabrication: Exclude the pre-fabrication of valves or flanges, prefabrication work must use a lot of labor to measure, cut, grind, weld, grind, and the latter part of the testing, including RT / NDT, X-RAY test, etc., are necessary processes. Take example of a set of "straight pipe + elbow" welding. In addition to the operations of transport/fake fixing/grinding, it is necessary to carry out the ring welding manually. The required welding time varies depending on the pipe diameter and wall thickness, and may be spent 0.5 hours to several hours. (Note: The pipeline material is limit to the common ASTM A53/A106, etc. for easy discussion) (see Fig. 1-2)
(3) Installation and construction: The prefabricated pipeline parts of straight pipe & elbow materials carried to the construction site, and assembled thems. Unlike pipeline prefabrication work in prefabricated yards/factories, pipeline parts can be overturned by machine/manpower and fully processed at all angles. On-site pipeline installation and assembly work in site is often limited by facility location, angle, and situation of work platform ,etc., will result in great quality differences in each installed product. (See Fig. 1-3) Most importantly, sometimes the welder cannot properly perform the installation because of the space limitations or angles of the mounting points, which may result in the welding quality being inadvertent and sometimes impossible to test. In addition to delaying the speed of installation work, after completion, the pipeline contents are constantly flowing, which is particularly prone to rust at some poor quality solder joints, resulting in an increase in future maintenance work (year-old repair or temporary repair). Increase costs. In addition, these shortcomings are extremely prone to sudden unexpected events, damage to human life and loss of property (see Fig. 1-4).

Fig. 1-1: Traditional elbow material (when the quantity is large, it will pile up everywhere)
Fig. 1-2: Prefabrication of pipelines in traditional contractor’s factory (still relying heavily on professional welders/labors)  Fig. 1-3: Fake fixing method used in traditional installation(site) elbow/pipe (the inner weld bead often has internal defects and residual stress)  
Fig. 1-4: traditional site breakage repair and leakage (left) and perforation leakage of the parent material of the bead line (right)
1.2 Missing of various sub-items of piping work
In the implementation of piping work, the main sub-items still have the following shortcomings for discussion: (1) Material procurement: In addition to valves, the main purchases are straight pipe and elbow. (i) Straight pipes and elbows should be purchased separately: Since most straight pipes are ordered from the big dealers, the elbows must be purchased from the processors. A variety of different procurements will generate a lot of management costs and troubles. (ii) Elbow purchases (delivery) are slower: Materials of Straight pipe, generally are conventional products can be purchased at any time from market. The elbow is processed from the straight pipe by the processor. Except for the material purchase and transportation, in addition to the necessary processing time, the processing must be determined according to the production schedule of the processing line. If it is urgently needed and there is no stock, there are requirements for inserting orders, which is quite troublesome; when the demand for elbows is small or the specifications are special, it is more troublesome; in addition, there are processes such as replacing the processing die set. In the process of prefabrication or installation, if there is a lack of elbows (especially special specifications), it will happen if it is to be worked or replaced by other products. (iii) Elbow delivery must be counted, space required for stacking, and sorted for easy access: After all, the elbow material is metal, and the weight is heavier. The large-size elbow is often difficult to move by hand, and sometimes it needs to be matched with the machine. Elbow material prices are more delicate, small-size elbows are easy to be lost for the workers or outsiders, and the warehouse management must pay attention, otherwise it will cause delays in follow-up work (prefabrication or on-site). (2) Prefabrication of pipelines: taking "straight pipe + elbow" welding in the contractor's factory as an example: (i) Welding work shall be carried out by labor: Heavy-duty piping (for example, industrial piping at the petrochemical plant), as the flowing liquid or gas in the pipeline is at high pressure, the pressure inside the pipeline is very large and cannot be combined with a simple screw casing ways to transport. Industrial piping has certain risks in normal operation, so the piping welding work is particularly important. The welder must be specially trained (usually shall be certified); and the more important pipeline welding welders must often be experienced by experienced welders. Labor costs are not cheap. The use of labor, correspondingly, must have labor, health insurance, accident insurance costs, and other necessary expenses. (See Fig. 1-2) In addition, in the case of pipeline welding with special materials (such as TI tubes, special alloy steel tubes, etc.), it is necessary to have a special training qualified professional welder to cooperate, or to perform additional commissions, and the cost is higher. (ii) Welding work shall be carried out with electrodes: In addition to the base metal, the welding work must have the need for welding rods, and the cost of the welding rod must exist. In the use of welding rods, manual material picking, heat preservation, and material consumption will inevitably lead to higher costs. Special material welding rods are more expensive. (iii) Welding work must spend a lot of time: Pipe welding time is generally related to the length of the weld bead, the thickness of the weld, and the number of weld layers. The more time. It must be related to labor costs unless automated machine tools are used. On the heavy-duty piping, all are carried out by manual welding, which is inevitable, the labor cost is high, and the construction period is long. (See Fig. 1-5)
Fig. 1-5: In traditional prefabrication, a large number of professional welders must be used
(iv) The welding work must be carried out with sufficient land or space: Manual welding cannot be done instantaneously and stay to work for a long time. Pipe fittings are laid and the contractor's factory needs to have enough land (open-air) or shop space (indoor) to meet. If the land/space is insufficient, it must be overtime/shift work, the cost will increase, the construction period will be lengthened, and the quality will decline. (See Fig. 1-6)  Fig. 1-6: In traditional prefabrication, using a large number of plants or space
(v) The results of the welding work must be verified: Industrial piping welding is an important task. In addition to the self-inspection of the contractor, the owner or the main contractor often has to station the factory supervisor and the inspection manpower. It must also have an outsourcing third-party inspection agency to carry out inspection procedures such as PT/RT to prevent improper quality of the construction that will cause accidents in the operation of the owner's factory in the future, and it will not be lightly responsible for major accidents. These necessary procedures will increase costs and lengthen the construction period. (See Fig. 1-7)  Fig. 1-7: A large number of X-RAY inspection procedures are required for traditional prefabrication
(3) Installation: Carry the prefabricated parts and straight pipe/elbow materials to the construction site and install them on site. (i) A large amount of welding work is required: The general site installation is similar to the contractor's factory prefabrication, except that the work location is at the site. Of course, different measures are derived from the local conditions. The amount of welding on the construction site is proportional to the number of joints required for the pipeline. The fewer the joints, the less the welding amount, the lower the cost and the shorter the construction period. Of course, the quality is higher (this is why the factory prefabricated quality is better than site installation as an example). (ii) Site welding quality may be affected by space limitations or angles: After all, the welding of the site must be carried out manually, and the welder will be subject to multiple restrictions on the working space, human limbs and welding tools. When the angle is not good and the space is crowded, the welder's welding quality will be affected and reduced, and the completion period will be correspondingly lengthened, and the cost will increase accordingly (see Fig.1-8). This is even more evident in the piping work or maintenance work carried out in the ship's cabin.  
 Fig. 1-8: Pipe welding quality is controlled by narrow spaces and working environment
2. Advantages and disadvantages of the new "quick heavy cold pipe bending" technology As mentioned above, the traditional industrial piping is still a deficiency. The newly developed "Quick Heavy Cold Pipe Bending" technology (hereinafter referred to as "quick pipe bending") is used to improve the traditional piping method to reduce costs, shorten the construction period and improve quality. 2.1 Operation principle and method of quick-heavy-cold-pipe-bending technology
Thanks to the advancement of modern technology, modern industrial piping drawings have been digitized (referring to AutoCAD drawings, or other soft-system diagrams, such as the common PDMS/PDS in Taiwan). The specific transfer to ISO drawings can also be easily used by other manufacturers/collaborative staff to read. This is a modernization of the design/drawing work, which greatly reduces manpower and improves the quality of the design/manufacturing interface. However, on the actual construction side, including the contractor's factory prefabrication and site installation, there was no major progress, and it still remained in the use of a large number of manpower (including professional welders and other auxiliary manpower). The development of the "quick-heavy-cold-pipe-bending" technology is to improve the old piping work method to save manpower and various costs. The operation principle of the quick-heavy-cold-pipe-bending technology is mainly to use a large-scale hydraulic processing machine with precision (see Fig. 2-1) to directly cold-bend the straight pipe material into a pipebent of specific angle. It is still connected to the other straight pipes on front or rare point (cutting can be processed according to requirements). A length of straight pipe can be processed into a continuous composition consisting of several bents and straight pipes (see Fig. 2-2). Newly developed quick-heavy-cold-pipe-bending technology, the machine has CNC bending machine, NC bending machine, etc. It adopts professional customized manufacturing and can reach the bending processing technology of R/D=1.5 times of industrial-grade pipe long-diameter elbow. 
 Fig. 2-1: CNC machine for Quick-heavy-cold-pipe-bending

   Fig. 2-2: finished example (continuous bent) for Quick-heavy-cold-pipe-bending
Originally, this cold-worked pipebent was used to bend small-diameter thin pipes. As modern processing tools(machines) have gradually become larger, the applicable outer diameters of the curved pipes are larger and the walls are thicker. At present, it only lists up to 5" Φ pipe diameter, and soon it can reach 10" to 12" Φ pipe diameter (see Fig. 2-3). The product is used in petrochemical plants and technology industry industrial pipeline cold bending heavy processing (carbon steel pipe, stainless steel pipe, alloy steel pipe, etc. are processed and bent.) The applicable diameter of the steel pipe is from 0.5" to 5" Φ, and the bending capacity is from 5S to XXS.
 Fig. 2-3: suitable thickness table (1/2" to 5" pipe grade) for quick pipebent
In the quick bending operation, the most important thing is the roundness and thinning rate of finished products(pipebent) in the bent section (see Fig.2-4). The data under actual cold work implementation is no worse than the purchased bend requirements.
 Fig. 2-4: roundness and thinning rate for Quick bent
In the production of traditional elbows, in addition to the large-diameter outer diameter elbows, the method of splicing welding (commonly known as shrimp pipe) is mainly used for heat treatment of elbows (high-frequency heating), as well as cold-working die extrusion. The method depends on the material of the pipeline and the thickness of the pipe. Generally, the most worrying aspect in pipeline design is the problem of residual stress in the pipeline of the quick pipebent. In fact, in the traditional piping process, in addition to the residual stress remaining in the processing of the elbow material in the processing plant, the residual stress caused by the high-temperature joint of the straight pipe and the elbow joint welding is not less than the residual stress; The damage left by the welding to the pipeline body is greater, and there are more problems remaining in the maintenance and repair in the future operation, and there are more hidden dangers. Our company's quick bending technology uses large processing tools for cold bending and high precision. With high-power bending machine, high-precision and complex diameter mold, guide mold, clamping mold, and core parts, under the control of adjustable speed digital position, it is possible to bend the pipebent without welding. Under the digital control processing, the quick bend can also bend out the combination of various angles, which is beyond the reach of traditional elbow. (See Fig. 2-5)    Fig. 2-5: Quick bend, thick pipe capacity and various angles (2"_160S_SS304)
At present, general piping is also used in the form of cold-worked pipebent, but most of them are curved pipes with a curved diameter of 3DR (commonly known as a large bend). This is because the previous processing machine still has technical deficiencies, and can only bend the curved pipe with a large bending diameter, which will have a great influence on the piping space. In the piping of petrochemical plants, due to technical requirements and space requirements, the elbows are mostly 1.5DR (commonly known as long-diameter elbows). Therefore, the traditional tool/machine of cold-bending is not suitable, and only elbow-welding can be used. Our quick bending technology utilizes the latest large processing machine, which can be used to make a straight bend with a small bend diameter of 1.5DR. The minimum can reach the bend diameter of 1DR (commonly known as short-diameter elbow) (all depending on material and pipe size. The machine is a machine, but not a panacea), which can meet the needs of petrochemical plants.
2.2 Advantages of quick-heavy-cold-pipebending technology
The appearance of a new technology mean that some existing shortcomings of the old technology can be improved, or simplified, or improved. The quick-heavy-cold-pipebending technology has the following advantages: (1) Quick bending can save processing time: Traditional industrial piping "straight pipe + elbow" joints are all welded by a professional welder. The welding time varies with pipe diameter, wall thickness and pipe material. For example, in the case of the common ASTM A106 2"Φ sch.40 pipe, a ring welding process takes about 0.5 to 1.0 hours, including professional welders and auxiliary labor. Other handling, false fixing, pipe grinding and dressing, bead grinding and dressing, etc. Time is also required. In addition, it is necessary to add the time required for various types of inspections (depending on the contracting requirements). If the ends of the elbow are to be joined to the straight pipe, it takes twice as long.(see Fig. 2-6) The new type of quick-bending pipebent processing, as long as the straight pipe is processed on the machine, the ASTM A106 2”Φ sch.40 pipe is taken as an example. One pipebent (the bent is connected to the straight pipe at both ends) is almost It can be completed in 10 to 30 seconds. The bending process is completed, completely controlled by the program digits, and the precision is not misplaced. This advantage is almost a microcosm and representative of all the advantages of the new "quick-bending” technology. Other advantages, let's continue.
  Fig. 2-6: Comparison of traditional piping welding and quick-bending operation (same 4” 40s CS pipe)
(2) Quick-bending can save the purchase of traditional elbows and save costs: The traditional industrial piping “elbow” must be purchased separately. Since the elbow is more expensive than the straight pipe, it will increase the cost. Moreover, the procurement delivery schedule of elbow parts will obviously be longer than the straight pipe purchase. Quick-bending technology directly adopts the straight pipe and pipe bending process, which can obviously save a lot of elbow costs. The direct processing of straight pipe into a curved pipebent can also reduce the loss of material of the straight pipe material, the benefit is obvious, and the speed of purchase and delivery is also fast. The material of these quick bends is the same as that of the straight pipe, and there will be no mistakes in material misconnection. Using precision machine processing, the pipebent can be directly digitally precision machined regardless of the 90°, 45° or other special angles. It is no longer necessary to cut the elbow secondary, saving cost and shortening the construction period, and improve quality. The quick-bending can always make the pipe into a continuous pipebents, saving processing time and materials. The traditional industrial piping is fixed in a similar way with the "straight pipe - elbow - straight pipe - elbow". It is determined that each elbow must have a ring weld at both ends, and it is also destined to waste more time and increase the cost. The new type of quick-bending processing can be used to continuously bend the pipe on the machine and continuously bend the pipe into several "straight pipe + elbow" type; of course, this will be limited by the size of the machine, the bending limit and the purchase straight, pipe length, etc. Standard industrial piping, especially for pipeline of multi-pipes, is usually turned in the same way as "bend and turn", so there must be multiple continuous bends on the path. The quick-bending technology can produce the required continuous bents, and the two ring-shaped joints are saved at each bent, which has obvious benefits. (See Fig. 2-7)   Fig. 2-7: Quick-bending, this continuous bents can save 8 ring-welds (left), various angle bents (right)
(3) The continuous bents of the quick-bend can stagger the joints that are not easy to weld, which can improve the quality: The traditional industrial piping is fixed with the “straight pipe-elbow-straight pipe-elbow” parts. When it is transported to the construction site, many site contacts may be located in a space-constrained location, and the overall quality will be poor. Quick-bending processing can use the method of continuous bending to try to stagger the places that are difficult to weld when the future construction site is installed, which can improve the quality. Also, because of the technology of continuous bending, the number of welded joints installed on the construction site is reduced, and the overall construction cost is also reduced and the construction period is shortened. This feature is especially suitable for extremely narrow spaces, such as ships and cabins that are not easily welded. (4) The quick-bending prefabrication work can be processed for 24 hours/day: After all, traditional industrial piping prefabrication is limited to human physical fitness, family life, lighting, weather, labor laws and regulations, and working time has its limits and restrictions. Quick-bending processing, using modern high-tech/higt-precision processing machine, as long as the power is supplied, it can be processed for a long time with few manpower. In theory, it can work 24 hours (of course, even the best machine still need maintenance), saving time and cost. This is a shortage of manpower in the Taiwan industry today, especially in the industrial piping industry where professional welders must be employed. The quick-bending process can use least manpower for prefabrication operations with obvious benefits. (5) The quick-bending prefabrication can be completely processed in the factory: The prefabrication of traditional industrial piping is limited to the contractor's workplace. The outdoor construction (pre-fabrication) would be partially used, and it is also affected by some weather factor (the welding work is susceptible to rain). The quality is easy to be different. Quick-bending processing, using high-tech/high-precision machine, can be almost completely operated in the shop, even in the rainy season, the quality stability is high, and the stability of product quality would not effected by continuous working for a long time. (6) Quick-bending preforms stable quality: The traditional industrial piping prefabrication stay in manual work, and the finished product will be limited by the professional welder quality of the contractor/sub-contractor. The quality of the finished product may vary depending on the quality of professional training of the welder. In addition, the contractor may be forced to temporarily adjust/dispatch, and be a veteran due to factors such as rushing work, worker mobility, and even worker resistance and labor disputes. Usually, outsourcing/re-subcontracting operations, etc., affecting quality and delivery. Quick-bending using modern high-tech/precision machines, almost got the same finished product quality, which is the characteristics of mechanical production, although it can not reach the highest level of production of light-less, but compared with traditional production methods, it has been greatly improved. (7) Pre-fabrication of quick-bending with less manpower, more professional training and stable quality: Traditional industrial piping prefabrication must use a lot of manual operations. The physical load of the staff is large and the flow of personnel is large. The contractor must continuously recruit and train the welders, which is easy to have quality differences. Quick-bending use modern high-tech/precision machines, the use of labors is almost minimized. This high-precision processing machine must be operated by professionally trained personnel. Due to the less manpower, it is easy to concentrate on training. And the working place is the indoor work(shop), the staff is stable, the mobility is low, the quality is easy to check, and the technology is easier to accumulate. (8) Quick-bending prefabrication is centralized operation, other machines in the vicinity of the machine in the factory are complete, and the operation efficiency is higher: Traditional industrial piping is a manpower-concentrated work. Even if it is prefabricated at the factory, it must be deployed in a large area of land/space. Although the use of machinery (such as spreaders, stackers, etc.), the benefits are difficult to develop. Quick-bending processing, the main operations are concentrated in the vicinity of the processing machine, plus the use of other equipment to assist, the efficiency is obvious. Modern factory management pays attention to machinework to reduce manpower, improve efficiency, and reduce costs. This would be better with the quick-bending technology. Conventional industrial piping prefabrication still requires a lot of welding on joints of "straight pipe-elbow" (ring-weld). In fact, the weld of interface is the weakest point of the entire pipeline. Quick-bending directly bends straight pipe into curved pipe or continuous curved pipe. Without welding, the quality of finished products can be ensured. Of course, this does not mean that the quick-bending process does not need to use welding, but can minimize the amount of welding and improve the quality. (See Fig. 2-8)  Fig. 2-8: Quick bending, the inner surface of wall of pipebent is very smooth (4"_40s & 2"_80s CS PIPE), no weld
(9) Pre-fabrication of quick-bending, better quality, less inspection and less cost: Prefabrication of traditional industrial piping, using a large number of welding, the finished product is still in need of inspection to ensure quality standards. Quick-bending has not any welding at the joints of bent and straight pipe (the welds of this interface of pipe/elbow is the weekest points in pipeline), and no welding inspection is necessary. Although the quick-bending is mechanized production, there are still few bad product that caused due to improper operation, such as wrinkling. Most of the inspections can be checked by visual inspection and touch. This advantage also affects the inspection of future site installations, as the number of welds in the quick-bending pipe is less and the amount of site installation inspection is less. (10) Quick-bend prefabrication, the joints installed on the site can be arranged in the straight pipe section, and the bent joint is staggered: The construction of traditional industrial piping will generally place the welds at the "straight pipe-elbow" joints to reduce the amount of ring-welds. This ring-weld is actually the weakest interface point in the pipeline. (Refer to Fig. 1-4) Quick-bending processing, directly making the straight pipe into a curved pipe or a continuous curved pipe. Since the original straight pipe has a certain length, there will be remaining straight pipe sections after bending, which can be utilized as much as possible to avoid material waste. Secondly, the joint welding of the "straight pipe-straight pipe" is always easier than the "straight pipe-elbow" joint, and the quality is better. But this advantage must be complemented by improvements in the design/manufacturing drawings to truly achieve economic benefits. (See Fig. 2-9)   Fig. 2-9: Quick-bending pipe is processed according to the ISO drawing (integral molding)
(11) Quick-bending, better fluid flow at the pipebent: Conventional piping has ring-welds at "straight pipe-elbow" joints, and these ring-welds are often the biggest barrier to flow in the pipeline. Quick-bending processing, there is no ring-welding at joint of straight pipe & bends, and the inner wall of the pipe in the pipebent is very smooth and has no weld bead, which will hinder the flow obstruction in the pipebent. It helps the owner's factory to produce process efficiency.
Secondly, the quick-bending, the maintenance and repair at the pipebent is low: Conventional piping will have ring-welding at the joint of "straight pipe-elbow", and these ring-welding is often the point where the owner's factory is most prone to rust, cracks, and operational safety accidents in the future operation. (Refer to Fig. 1-4) Quick-bending, there is no ring-welding at pipebents, it is not easy to have rust and cracks, which can reduce the incidence of operation safety accidents and reduce the loss of personnel/property/stopping of the owner's factory. Will also reduce the annual repair expenses. (See Fig. 2-10)   Fig. 2-10: There is no ring-welding process between straight pipe & bends (1.25"_160s_CS PIPE)
(12) Quick-bending, under the digital control, the same size and specifications can be used for a large number of high-precision product copying: The traditional piping must be welded one by one by hand, which is time-consuming and labor-intensive and has poor precision. With large machine and digital control, the quick-bending can copied in a large amount under the same specifications, which is fast and accurate. (See Fig. 2-11)   Fig. 2-11: Quick bending, which can be copied quickly, in large quantities, with high precision
2.3 Disadvantages of quick-bending technology
Having said the advantages of so many quick-bending techniques, it cannot be avoided, there are still some disadvantages. In fact, these are industrial inputs, they are not shortcomings, but they will become working capital in the future. (1) Quick-bending must cost the purchase of precision processing machines: If a worker wants to do something good, he must first sharpen his tools. Without high-tech /precision machining machines, quick-bending technology cannot be implemented. The price of these precision processing machines is not low, and it must be invested huge amounts of money in advance. (See Fig. 3-1) (2) Quick-bending operators must be trained by professional operators of processing machines: Initially, the basic operational capability was established by professional training of processing machine manufacturers. Secondly, the operator's experience and accuracy are honed through the actual operation in the factory. It cannot be rumored that this is a necessary cost of consumption. But thanks to high technology, we have been able to save a lot of training time and costs for oper.ators. In addition to the quality of the finished product, the well-trained operators can also reduce the ratio of defective products. After all, the precision machine is also required to operate. (See Fig. 2-12)   Fig. 2-12: Good pipebent (left), bad products/wall wrinkles (right)
(3) The consumables of the quick-bending machine are quite expensive: The large-scale machine used in the quick-bending of the pipe for heavy industrial pipelines, because of the large power, the loss of the parts. These consumables are not expensive. (See Fig. 2-13)  Fig. 2-13: Quick bending machine fixture consumables
(4) Quick-bendings must establish unique technology KNOW-HOW: In the fiercely changing modern industry competition, organic stations and personnel can not survive only by relying on the manufacturer's machine manual. The unique technology KNOW-HOW is the keypoint of sustainable operation. In addition to the introduction of machine tools and personnel, there is also a need for deep technology to raise the competitive threshold. This paragraph is deeper and will be discussed later. (5) Some special pipes are still required to be supplied by the owner or the main contractor: Since the quick-bending is a part of processing, the financial resources are limited, and the procurement line is also limited. Therefore, some special straight pipe materials (materials or pipe diameters) are still required to be supplied by the owner or the main contractor to be bent. Some materials of special pipelines have long delevery times, or must be purchased from abroad, and are not suitable. (6) Some special pipes can not be processed by quick-bending: The quick-bending is processed by a large machine, but the machine energy and the matching mold have limitations, and cannot provide comprehensive bending processing. E.g: (A) At present, the maximum processing pipeline size is 5”~6” diameter. If it exceeds, it can only be used in traditional elbow ring welding. We are heading towards the development of the 10"~12" diamenter processing machine, which will be gradually overcome in the future; however, it will obviously not provide all the pipe diameter processing. After all, the market will speak. (B) Some of the extra-thick pipes cannot be bent. (C) Some special materials of pipes cannot be bent. (7) Quick-bending is also limited to the length of pipe: Straight pipe generally has its length limit (for example: 6 meters), which means that after the pipe bending process, the total length of the “straight pipe + bent” is not infinitely extendable, and the necessity of ring-welding must still be necessary. The excellent manufacturing design is to fully utilize the length of the pipe and try not to waste it. (See Fig. 2-14)
  Fig. 2-14: Used in LPG system, 4”_40S_CS PIPE quick-bending piping (above: the exist. pipe of the pipeline Tie-in. below: the modification of the underground pipe to the above ground pipe)
3. The conclusion
In fact, the general type of quick-bending technology has existed for many years, and is generally a small-sized pipe diameter and thin wall cold-worked bent, which is widely used in various industries. For example: handrailing pipe in the civil construction (commonly stainless steel pipes, 1.25" to 3" Φ mostly), electric heat exhaust pipe/tubes (such as electronic parts exhaust heat copper pipes, about 1/16", 1/8" diameter, etc.), the exhaust pipe of the steam locomotive, etc., it can be seen that cold bending is a reliable technology. Thanks to the advancement of digital technology and the help of advanced high-precision processing machines, the quick-bending technology developed by Dehan has further improved the above technology to a larger diameter (currently 5” to 6 "Φ machine, 10"/12" Φ diameter machine has been developed), the application surface is mainly industrial pipe with large internal pressure, especially the petrochemical pipeline. (See Fig. 3-1) The petrochemical industry is a technology-intensive, capital-intensive industrial construction with certain risks, and its products are widely used in various related industries. Nowadays, the newly developed quick-bending technology can reduce costs, shorten the construction period, improve the quality, reduce the inspection, and even reduce the maintenance frequency and cost after operation and the repair cost. The times are constantly moving forward and the environment is constantly changing. The demand of the owners is constantly improving, the prices are continuously reduced, the construction period is continuously compressed, and the work safety is continuously required to be improved. Traditional piping engineering has to use a lot of labor, a large number of parts, and a lot of time to complete, and it is gradually unable to catch up with the era. In recent years, the labor laws of Taiwan society have also been changed a lot and is transformed into another more serious situation in the future. The industry should recognize the challenges of the future. The rapid development of science and technology has brought digitalization and precision. Mechanized production methods and new business models. The "quick-bending" technology is sufficient to meet the needs of the current era and future.  Fig. 3-1: Cold-working CNC processing machine (front and rear sides)
We provide service:
[Professional Technical Service]: scope of quick-bending processing 1. Contract construction of the construction of piping project. 2. The manufacturing of 3-D drawing specifies the bending pipe. 3. Provide non-welded pipebent/elbow fittings. 4. Other added value. [Quick-bending Technology Advantage]: Cost reduction of the owner and improvement of pipeline quality 1. There is no need to spend the direct cost of purchasing to elbows. ...(cost down) 2. Save on non-destructive testing (NDT) and construction costs for elbow welds. ...(cost down) 3. Reduce the overall cost of the people involved in the on-site fire procedure. ...(cost down) 4. Reduce the risk of misuse of pipeline and elbow materials. ...(material quality control) 5. Omit the influence of thermal stress on the elbow weld. ...(reducing the amount of welding thermal stress) 6. Reduce the total penetration of the weld at the elbow to block the fluid disturbance! ...(no tube weld resistance) 7. Good in high speed fluid/low resistance fluid materials. ...(transportation is smoother) We adhere to the "professional technology, service-oriented, quality-oriented" approach to the concept of sustainable management. Talent and experience are the pillars of the project. We have accumulated more than 40 years of rich piping experience and engineering performance, and all personnel are professionally trained. Through continuous learning and accumulation of experience, we will provide you with the most professional, most complete and most efficient service quality, and hope for the support and advice of friends from all walks of life.
Technical inquiry: email: service@dehantech.com Manufactory: Company: Ying Zhang Industry Co., Ltd. (Business ID: 8930 2767) Address: No. 3-1, Lane 226, Wenxian South Road, Linyuan Dist., Kaohsiung City, TAIWAN Tel: (+886) 07 - 642 2576 / (+886) 0932-792-307 Mr. Yu Weiqing/General Manager Fax: (+886) 07 - 643 6184 E-mail: a89302767y@gmail.com also see: website, Facebook
Download: Brief Introduction to DH Quick-bending technology - PDF file (Traditional Chinese) , (Simple Chinese version) (upd@ 2017-07-02) , (English version)
|